地域に根差すスーパーによる、サーキュラーエコノミー構築へのチャレンジ 株式会社フジ 松山デリカPC(プロセスセンター)/ A Local Supermarket Tackles the Circular Economy: Fuji Co., Ltd. Matsuyama Delica Process Center / 扎根地域的超级市场,构筑循环经济的挑战——株式会社FUJI Delica PC(流程中心)
社会的にSDGsが意識されるようになり、各所で循環型社会への転換が模索されていますが、私たちの暮しに関わる企業では、どのような対応が進んでいるのでしょうか?
愛媛県民にとって最も身近な企業の一つ、スーパーを展開する(株)フジ。同社の松山デリカPC*は、中四国のフジ全店約100店舗で販売する惣菜(弁当、サラダ、カット野菜等)を製造しています。(*2024年3月の組織変更により、(株)フジデリカ・クオリティが親会社に統合されて同センターとなりました)
同社は、日頃より廃棄物削減への取り組みを進めてきました。中食需要の拡大に対応し、出荷量増加による工場の増設、設備更新を行うタイミングで、製造工程で発生する食品残渣を有効活用するバイオマス発電プラントを導入し、2020年2月より本格運転をスタート。中四国民間企業初となる、自社食品残渣のみを利用するバイオマス発電プラントでは、1日当り約5トンの食品残渣から約800kWh/日を発電して、電力会社に売電しています。
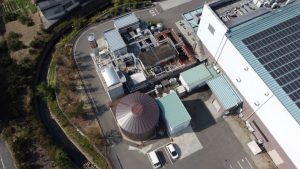
バイオマス発電プラント全景。右側の建物は惣菜製造工場
■食品残渣を活用したメタン発酵バイオマス発電
導入したのはメタン発酵バイオマス発電プラント。惣菜等の製造過程で出る食品残渣を破砕し、水分調整後に大きな円筒形のメタン発酵槽に貯め、有機物を分解する際に発生するメタンガスを燃料にして発電が行われます。投入する食品残渣の量や種類による負荷の変動があるため、当初は処理が安定せず、メーカーからのアドバイスを得ながら運転を行ったそうです。これまでの運転ノウハウの蓄積により、現在では安定的な稼働が維持されています。食品残渣の投入以外は、ほぼ全自動であり、処理作業の手間は省けているそうです。
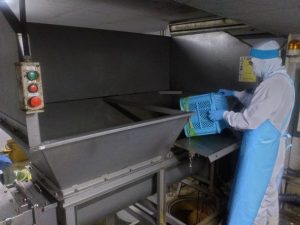
粉砕した食品残渣を発酵槽に投入します
このシステムの導入によって、食品残渣処理委託費約1,500万円(年間)が削減され、売電収入約1,100万円(年間)、廃液の処理費用や設備の維持費用約1,000万円(年間)との収支で、年間約1,600万円のコスト削減となり、10年強でプラント建設等の初期投資額(イニシャルコスト)が回収される目途となっています。
また、排水処理においては、2018年度に嫌気の環境下での排水処理で有機物をメタンガスとして回収するシステムを導入。メタンガスを熱エネルギー(蒸気)に転換して利用し、年間で約660万円のコスト削減効果が出ています。
■社会の反応を実感
「この工場からのゴミゼロを第一に考えており、環境負荷低減を実現していることをうれしく感じています。」と責任者は話してくださいました。
2020年度には愛媛県による優良循環型事業所として認定され、メディアで紹介される機会もあって、工場見学する自治体や企業が増え、循環型社会構築に寄与する企業として認知が高まったと感じているそうです。また、同じ認定企業との交流が進み、取引や連携へと発展しつつあり、ビジネスへの好循環も始まっています。
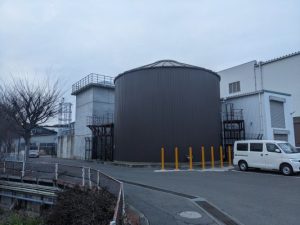
発酵槽(円筒形の建屋)
■さらなる環境負荷低減へ
惣菜等の販売は、売れ残りが食品ロスに直結してしまいます。そこでAIによる販売量の需要予測システムを導入し、AIの予測を基に販売計画を日々調整することによって、廃棄量を減らす効果を上げ、環境負荷低減に貢献するとともに、利益の確保につなげています。
さらに、食品トレーの重量削減による廃棄プラスチック削減にも取り組んでいます。同社も加盟する(一社)日本惣菜協会など業界団体や同事業者間でも、食品ロスや廃棄プラスチックの削減に取り組み、新技術の導入やノウハウの共有が進められているそうです。
社会やライフスタイルの変化に対応し、同社の惣菜製造事業は拡大しながら循環型社会構築に向けた多様な取組を展開していました。私たち消費者もこれらの取組を知り、相乗効果が高まるように、日々の「食」における行動を見直したいと感じました。
A Local Supermarket Tackles the Circular Economy: Fuji Co., Ltd. Matsuyama Delica Process Center
As society becomes more conscious about the SDGs, various sectors are searching for ways to transition to a circular economy. But what kinds of measures are being taken by businesses integral to our daily lives? Enter Fuji Co., Ltd., which operates a supermarket chain familiar to any resident of Ehime Prefecture. The company’s Matsuyama Delica Process Center produces ready-made meals (including bento boxes, salads, and cut vegetables) for sale in all of the approximately 100 Fuji stores in the Chugoku and Shikoku regions. (Due to an organizational change in March 2024, Fuji Delica Quality Co., Ltd. was fully absorbed into its parent company, Fuji Co., Ltd.)
Fuji has consistently strived toward reducing waste. When the company underwent factory expansion and equipment upgrades to increase production in response to an increase in demand for ready-made meals, it took the opportunity to install a biomass power plant that utilizes the food scraps left over from the production process. The plant came online in February 2020, marking the first time a private company in the Chugoku and Shikoku regions has operated a biomass power plant using only its own food waste. Every day it generates about 800kWh of electricity from roughly 5 tons of food scraps, which is then sold to the electric power company.
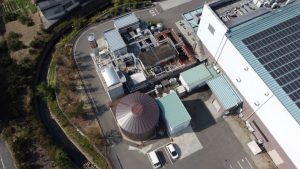
<Overview of the biomass power plant. The building on the right is the ready-made meal factory.>
■ Methane Fermentation Biomass Power Generation Using Food Scraps
The installed plant is a methane fermentation biomass power plant. Food scraps from the production of ready-made meals are pulverized, moisture-adjusted, and then put in a large cylindrical methane fermentation tank, where the decomposition of organic material produces methane gas used for power generation. At first the operation was unstable due to fluctuations in load depending on the amount and type of food scraps used, but the issue was resolved with guidance from the manufacturer. Accumulated operational know-how has enabled a consistent and, with the exception of loading the food scraps into the tank, mostly automated process, significantly reducing the amount of time and effort required.
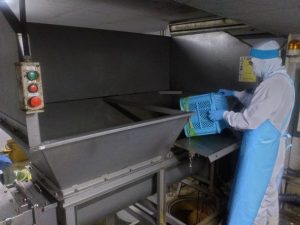
<Pulverized food scraps being fed into the fermentation tank>
The installation of this system has cut food waste disposal costs by approximately 15 million yen per year, while bringing in about 11 million yen per year from electricity sales. Even with the roughly 10 million yen per year in additional costs from liquid waste disposal and equipment maintenance, that still comes out to a net annual cost reduction of about 16 million yen, meaning the initial cost of constructing the plant is expected to be recouped in just over ten years. Also, in fiscal year 2018 a system was installed that captures organic material as methane gas during wastewater treatment under anaerobic conditions. This methane gas is converted into thermal energy (steam) and used, resulting in an annual savings of about 6.6 million yen.
■ Feeling Society’s Response
“I truly feel this factory’s commitment to producing zero waste and the success we’ve already had at reducing our environmental impact is something to be proud of,” says the person in charge. In fiscal year 2020, the company was recognized as an Excellent Circular Business Operation by Ehime Prefecture, resulting in increased media coverage and interest from local governments and businesses in conducting factory tours, and enhancing its reputation as a company contributing to building a circular economy. What’s more, exchanges with other recognized companies are opening the door to new deals and collaborations, initiating a positive business feedback loop.
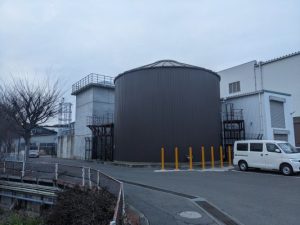
<Fermentation Tank (Cylindrical Building)>
■ Reducing Environmental Impact Even Further
When ready-made meals go unsold, it directly contributes to food loss. To combat this, Fuji has implemented an AI-based sales forecasting system, allowing them to reduce food loss by adjusting their sales plan on a day by day basis. This has helped reduce their environmental impact and secure profits. Efforts are also underway to reduce plastic waste by cutting down the weight of food trays. And, they are working with industry groups like the Japan Ready-made Meal Association (of which they are a member) and fellow retailers to reduce waste across the sector by promoting the introduction of new technologies and sharing know-how.
As society and lifestyles evolve, Fuji is expanding their ready-made meal business while simultaneously enacting various initiatives aimed at building a circular economy. I hope that by learning about these initiatives, we consumers are inspired to reconsider our own daily food-related behaviors and do our part to make their efforts more effective.
扎根地域的超级市场,构筑循环经济的挑战——株式会社FUJI Delica PC(流程中心)
随着社会意识到SDGs的重要性,各个地方都在摸索向循环型社会转变,与我们生活相关的企业在采取怎样的应对措施呢?经营超市的㈱FUJI是爱媛县民最熟悉的企业之一。该公司的株式会社FUJI Delica PC是为中四国地区富士全部100多个店铺制造销售用的熟食(便当、色拉、切好的蔬菜等)的公司。(根据2024年3月的组织架构变更,㈱FUJI Delica Quality被母公司合并成为该中心)。
该公司从平时都注意废弃物的削减。以应对在家食用的方便食品需求的扩大,以及因为出货量扩大而增设工厂、更新设备为契机,该公司导入了有效利用制造工程中产生的食品残渣的生物发电设备,从2020年2月开始正式运行。这是在中四国民间企业首个只利用本公司食品残渣的生物质能的发电设备,每天从约5吨的食品残渣中发电约800千瓦时,卖给电力公司。
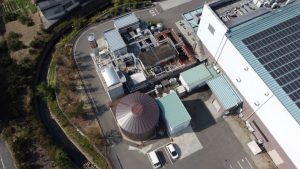
<生物质能发电设备的全景。右侧的建筑物为熟食制作工厂>
■利用食品残渣的甲烷发酵生物质能发电
该公司导入的是甲烷发酵生物质能发电设备。该设备将熟食等制作过程中产生的食品残渣破碎,经过水分调整后储存在巨大的圆筒形的甲烷发酵槽中,将分解有机物时产生的沼气作为燃料进行发电。由于投入的食品残渣的数量和种类会造成负荷的变动,最初的处理效果并不稳定,在听取制造商的建议的同时进行运转操作。从此以后,由于运转设备的经验积累,现在已经实现稳定的运转。除了食品残渣的投入以外,几乎都是全自动的,省去了处理工作的麻烦。
<将粉碎的食品残渣投入发酵槽>
通过导入这个系统,减少了食品残渣处理的委托费用约1,500万日元(年),售电收入约1,100万日元(年),废液的处理费用和设备的维护费用约1,000万日元(年),实现每年减少支出约1,600万日元,实现10多年时间完全回收设备建设初期的投资额(初始成本)的目标。另外,在废水处理方面,2018年度导入在厌氧环境下的废水处理过程中将有机物转化为沼气回收的系统,将沼气转换成热能(蒸汽)加以利用,每年可消减约660万日元的成本。
■感受社会的反馈
负责人介绍说“我们首先考虑的是工厂垃圾的零排放,实现环境负担的降低,对此我们感到很高兴。” 2020年度该公司被爱媛县认定为优良循环型事业所,有机会在媒体上进行了介绍,参观工厂的自治体和企业也在增加,作为循环型社会构建贡献企业的认知也在提高。另外,获得同一认证企业之间的交流也在不断推进,逐渐向交易和合作的方向推进,商业上的良性循环也已经开始。
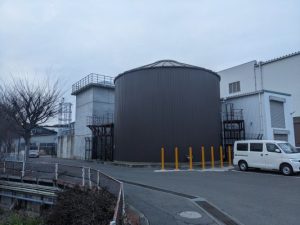
<发酵槽(圆筒形建筑物)>
■进一步降低环境负荷
熟食等的销售,卖不完会直接导致食品损失。因此导入了基于人工智能的销售量需求预测系统,根据人工智能的预测每天调整销售计划,实现提高减少废弃量的效果,为降低环境负荷做出贡献的同时,也确保了利润。在此基础上,通过减少食品托盘的重量等工作来减少废弃塑料。该公司也加入的日本熟食协会等业界团体和同事业者之间,也致力于减少食品损失和废弃塑料的事业,在新技术的引进和经验的共享等方面持续推进。
为适应社会和生活方式的变化,该公司在熟食生产事业不断扩大的同时,为构建循环型社会开展了多种多样的工作。我们消费者感到在知道这些工作的同时,为了提高协同效果,想要重新审视每天在“饮食”方面的行为。